US 24V GC267Ah
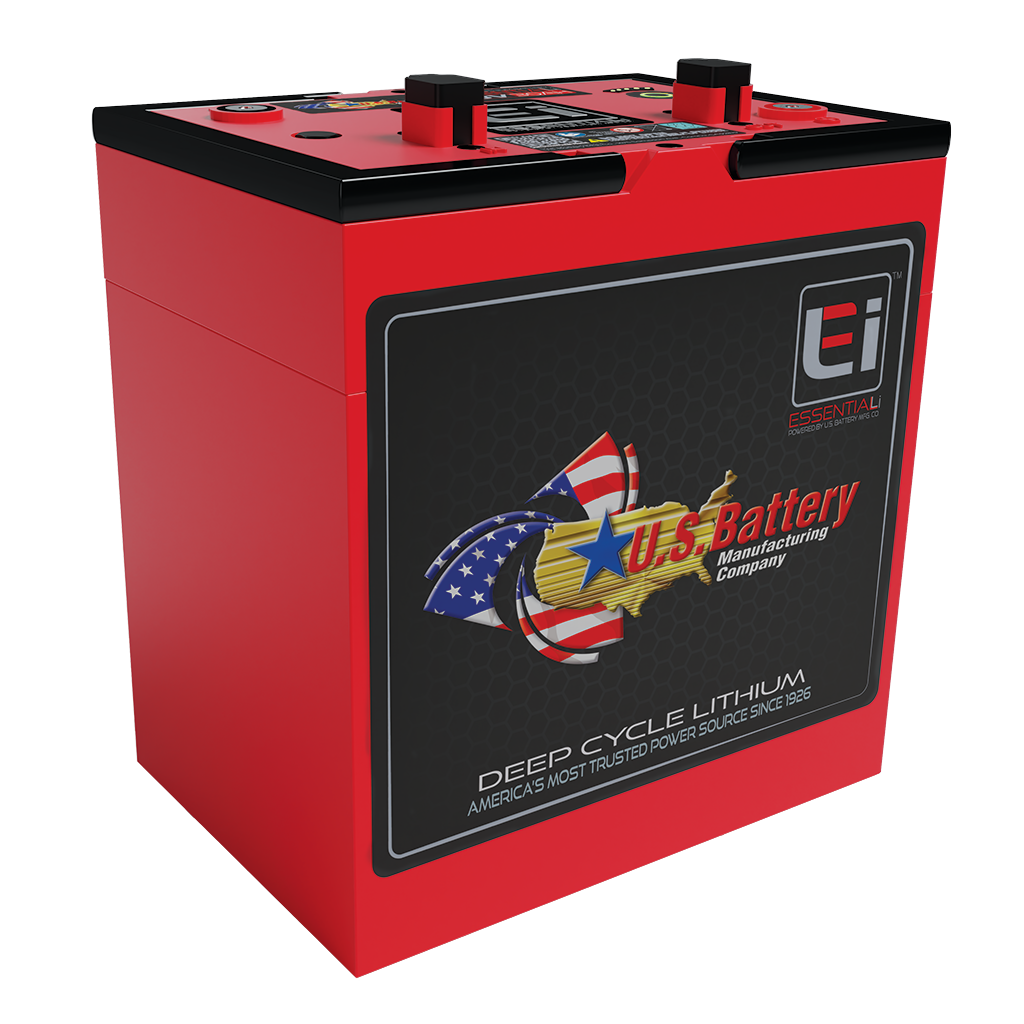
US 24VGC2 Voltage 25.6-Volt Deep Cycle Lithium-Ion US 24VGC2 Dimensions Length: 10.24” (260mm)Width: 7.09” (180mm)Height: 11.04” (280mm) Weight: 32.2 lbs (14.6 kg) Type Lithium Iron Phosphate (LFP) battery Certifications UN 38.3UL2580 (Cells)UL2271 (Pack) 2025 San. Maintenance Honorable Mention Health & Wellness Award 2024 MSN New Carpet Care Product Award Application Wherever Maintenance-Free, Leak Proof, Deep Cycle […]
US AGM DIN20 Hour Rate: 225
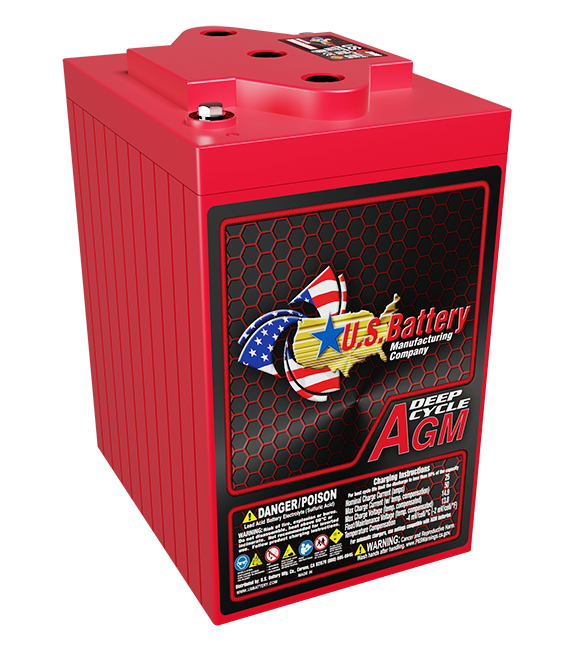
US AGM DIN Voltage 6-Volt Deep Cycle Sealed AGM Dimensions Length: 9.57” (243mm) Width: 7.38” (187.5mm) Height: 10.8” (275mm) Weight: 70.5 lbs (32kg) Type Sealed Non-Spillable Lead Acid (AGM) Application Wherever Sealed, Leak Proof, Deep Cycle 6-volt batteries are needed. Data 20 Hour Rate: 225 5 Hour Rate: 184 Minutes of Discharge @ 75 Amps: […]
US AGM L1620 Hour Rate: 414
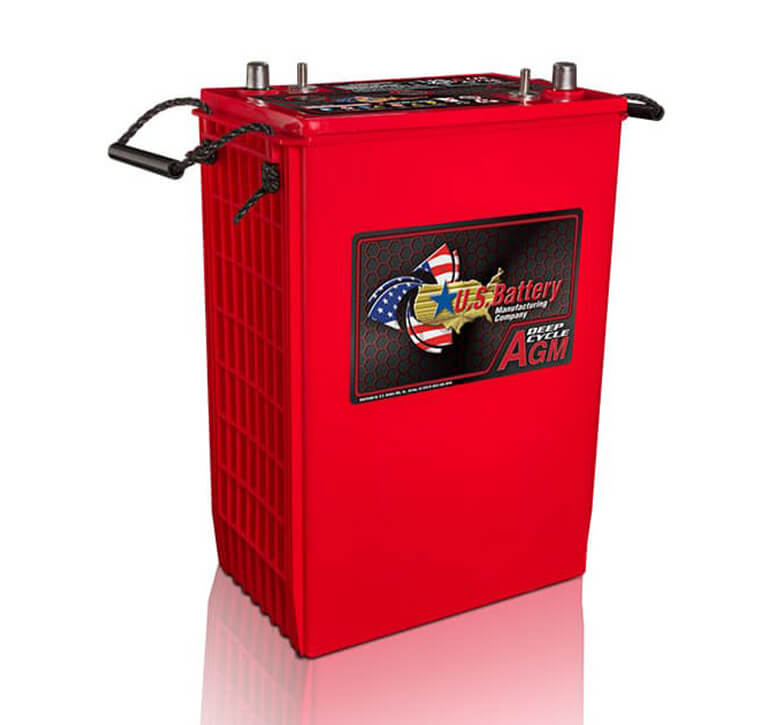
US AGM L16 Voltage 6-Volt Deep Cycle Sealed AGM Dimensions Length: 11.61” (295mm)Width: 7” (178mm)Height: 16.65” (423mm) Weight: 126 lbs (57kg) Type Sealed Non-Spillable Lead Acid (AGM) Application Wherever Sealed, LeakProof, Deep Cycle 6-volt batteries are needed. Data 20 Hour Rate: 4145 Hour Rate: 360Minutes of Discharge @ 75 Amps: 275Minutes of Discharge @ 56 […]